OPEN’s Control Manager
In OPEN’s New Measurements mode, the environmental control function keys (Figure 7‑1) allow control of fan speed, humidity (using flow rate), CO2 (with optional 6400-01 CO2 Mixer), temperature, and light (with optional 6400-02B LED Source, or 6400-18 RGB, or 6400-40 LCF).
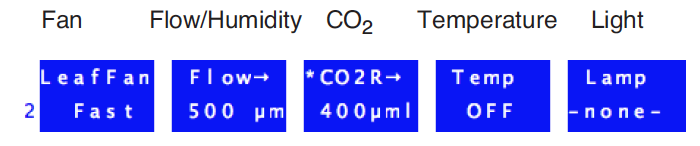
Four of the five control areas represented by the key labels above share a common control manager. The control manager is simply the software that defines the user interface and how and when the user’s selections are implemented.
Interface Fundamentals
Each control key label reflects the type of control, the current target, and the stability status. Pressing one of the four function keys brings up a configuration dialog for that control. The flow/humidity key (f2), for example, is shown in Figure 7‑2.
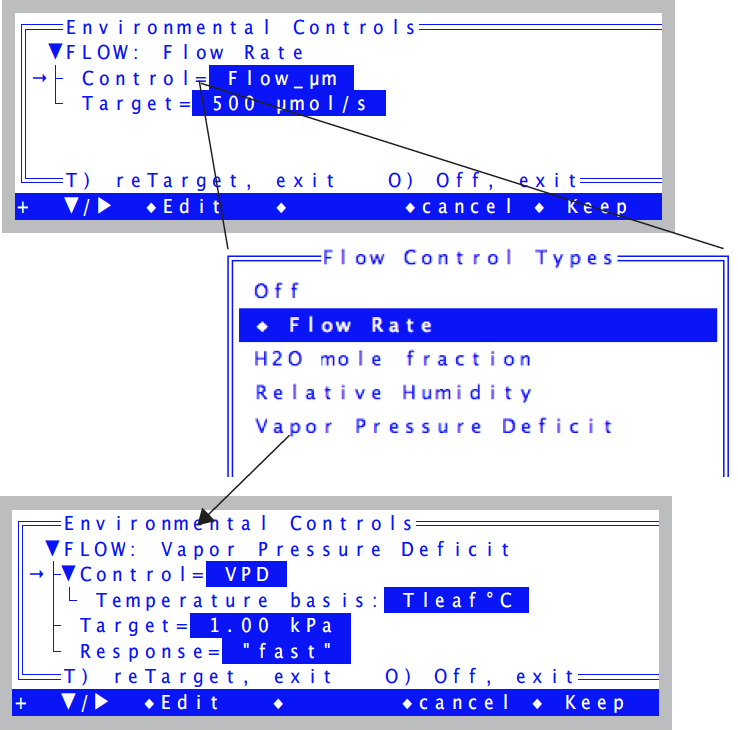
Normal procedure is to edit the appropriate nodes in the tree, and when it is to your liking, press Keep (f5) to implement the new control settings, or cancel (f4) to exit and leave the control unchanged.
Shortcuts
There are two shortcuts; T and O. Pressing T will immediately edit the target value (Figure 7‑3) and, unless you press escape to cancel, will then exit and implement the new settings. Pressing O (as in Off) does the equivalent of editing the Control= node, selecting the Off option, and then pressing Keep.
Editing the Target
When you edit a Target= node, the screen appears as in Figure 7‑3.

A blank entry (just press enter) will retain the current value. If you enter the letter c, the target will be set to the current value of the appropriate variable.
If you wish to enter a variable target, use the character #, either by itself, or with an ID value (e.g. #20). See Variable Targets.
Behind The Scenes
Once the user has specified a control and target, the control manager sets the appropriate hardware. The system then begins a regime of periodically checking the stability status and fine tuning the control as needed.
Each control option has three software components: a fast component that executes every 3 seconds, a medium component that executes every 10 seconds, and a slow component that executes every 30 seconds. These components are called interrupt service routines, or ISRs. A particular control may not actually use all three ISRs; this depends upon how much work is being done by the hardware, and on the response time of the quantity being controlled. ISRs execute at regular intervals while the control manager is active.
For example, the LED light source responds nearly instantaneously to control changes, so fine tuning adjustments to keep it at a target value can be done with the 3 second ISR, while the 10 and 30 second ISRs do nothing. Controlling leaf temperature, however, is a much slower process, so the 10 and 30 second ISRs are needed.
Active vs. Inactive Control Manager
The control manager is inactive when it is not doing the fine tuning necessary for target tracking. The consequences of this depend on the control. Some controls are fully implemented in hardware, leaving nothing important for any of the three ISRs to do1. Usually, however, the ISRs are important, and so it is important to know when the control manager is active, and when it is not.
When is the Control Manager Active?
The control manager is active in New Measurements mode (which includes AutoProgram activity), except during IRGA matching. The practical consequences of an inactive control manager are minor, at least over short periods of time. Some controls are implemented in hardware (such as block temperature control and null balance water vapor control), so even without the control manager, they will still actively track. The others will simply have stable targets that won’t be adjusted to account for changing temperature. Specifics can be found in the ISR descriptions for each control described below.
Variable Targets
Any control mode whose target entry box includes a message about a pound sign (#) after the default label (e.g. Figure 7‑3) can have a variable target instead of a fixed value target. For example, you may wish to maintain a relative chamber humidity that is the same as the humidity measured with an external humidity sensor. Rather than entering a number for the target, enter a pound sign
#
and press enter. You will be shown a list of system and user defined variables, from which you can pick the quantity that is to be tracked.
Alternatively, if you know the ID number for the system variable or user variable, you can enter it directly and bypass the menu selection.
#-13
(Variable number -13 is the external quantum sensor, for example.) When a variable target is specified, the target is updated every 30 seconds, but only while the control manager is active.
Example: Tracking External Humidity
Suppose we want to make chamber humidity track a value2 provided by user channel #1001 named xtrnRH. Once this is all configured (Chapter 15 in the instruction manual), we can press 2 f2 (i.e. f2 in level 2) to select the flow/humidity control, set Control to Relative Humidity, edit the target and enter #1001 enter (Figure 7‑4). Or, you could just enter # and pick xtrnRH from the menu.
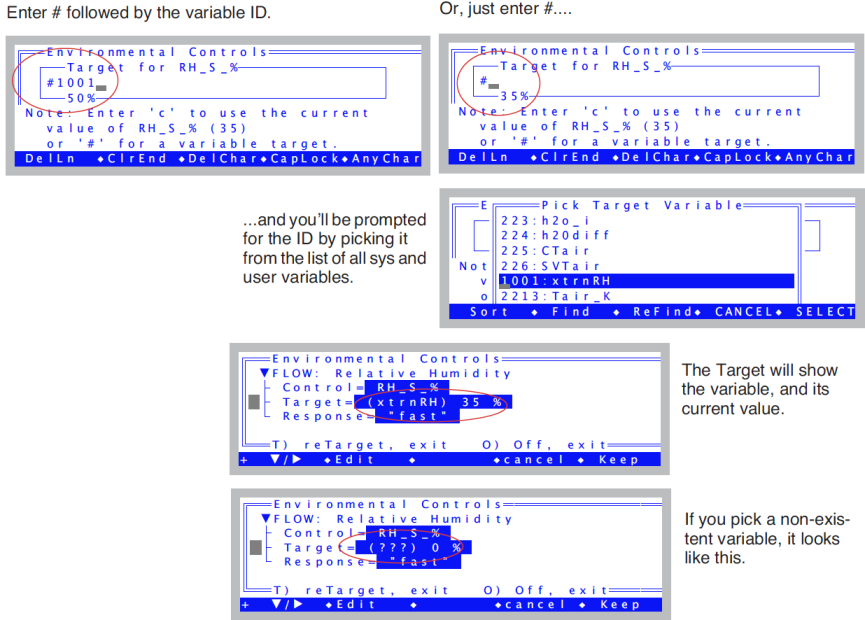
Then, the flow/humidity control function key will show the humidity target as the latest value of the variable we specified.

When a control has a variable target, the 30 second ISR for that control is skipped; instead, the control manager retargets the control to the current value of the specified variable. The end result is that every 30 seconds while the control manager is active, the target for the control will change.
Variable targets are a powerful tool, but do have a possible limitation when combined with AutoPrograms. See AutoPrograms and the Control Manager on page 25-30 in the instruction manual.